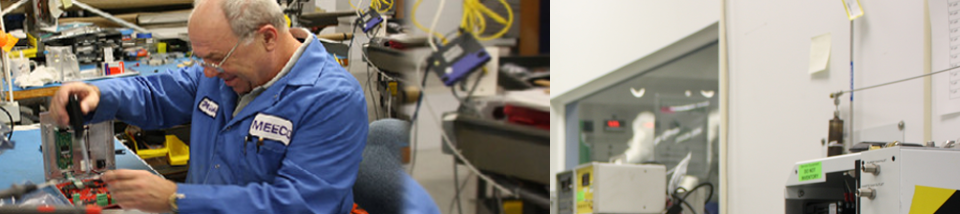
Is Routine Maintenance Performed on my Returned Unit?
Welcome to the MEECO Compliance 9000 Program! This extended warranty program was developed to help you meet ISO 9000 requirements on your MEECO moisture analyzer.
Service and maintenance will be performed by qualified technicians at MEECO’s factory or on-site at your location. The Compliance 9000 Program covers repair parts (excluding consumables) and labor; calibration and certification using N.I.S.T. standards; annual N.I.S.T. certificate; accelerated turn-around for cleaning and resensitizing of one cell per unit per year. If your cell cannot be cleaned and resensitized, you will receive a new cell free of charge, at MEECO’s discretion.
Loaner units will be offered, subject to availability, while your unit is in for service. In addition to repair service, the following routine maintenance will be performed on each individual analyzer:
- electronic calibration of LED readout, 4-20 mA output and alarm (if used)
- calibration performed using a N.I.S.T. traceable current source
- mass flow controller calibration vs. N.I.S.T. traceable flow standard
- for high purity units, when required, verification of moisture cell response and accuracy using a permeation-based moisture generator
- static leak-check on industrial gas units
The estimated time to perform routine maintenance is six (6) weeks for high purity units, and four (4) weeks for all others. Shipping time is not included. Customer’s units returned to MEECO’s factory for service or maintenance will be prioritized on a first-in/first-out basis. All returns must arrive with a Return Authorization Number, and be packaged appropriately. Units must be shipped with inlet and outlet caps on.
If work is performed on a unit covered under this program prior to expiration of the first year, the unit will automatically qualify for the purchase of another year of extended warranty. Prior to the agreement’s expiration, a renewal notice will be sent. If your unit’s warranty, original or extended has expired, and it has been over one year since your unit has been in for service, a re-qualification check-up, performed by our Service Department, must be performed. This re-qualification will be at the normal per-unit service cost. Defective parts will be replaced at the customer’s expense. After the instrument is repaired and re-qualified, it will then be eligible for the Compliance 9000 extended warranty program.
The Compliance 9000 Program cost does not include travel expenses (food, lodging, airfare, ground transportation, and related freight charges) for field service. If on-site service is desired the customer will be responsible for all travel expenses plus a per diem charge.